The Importance of Achieving Uniform Cooling
When kilnforming glass, especially largescale work, it is important to cool the glass uniformly throughout the annealing range. The temperature difference within the glass—from top to bottom, side to side, or end to end—should be no greater than 10ºF (5ºC). Such uniformity prevents a number of problems, including the creation of annealing strain, which can lead to glass failure.
At Bullseye, to ensure uniform cooling and proper annealing of large-scale work, we monitor temperatures at multiple points within the kiln during firing.
Our multiple-point temperature monitoring system involves the use of thermocouples and a pyrometer. The pyrometer displays temperatures that are sensed by the thermocouples, which are placed at two or more locations within the kiln. (Figure 1)
Information gathered and displayed by the pyrometer indicates how the glass and the kiln are heating and cooling and whether kiln temperatures need to be modified to prevent annealing strain—either by adjusting heat output from the top, bottom, or side elements (if they are controlled separately) or by slowing the cooling rate. A multiple-point temperature monitoring system is well worth the small investment in equipment and energy required for installation.
In this document, we discuss when to employ such a system, the equipment that is needed, where to find the equipment, how to install it, and how to use the information gathered to help ensure successful annealing.
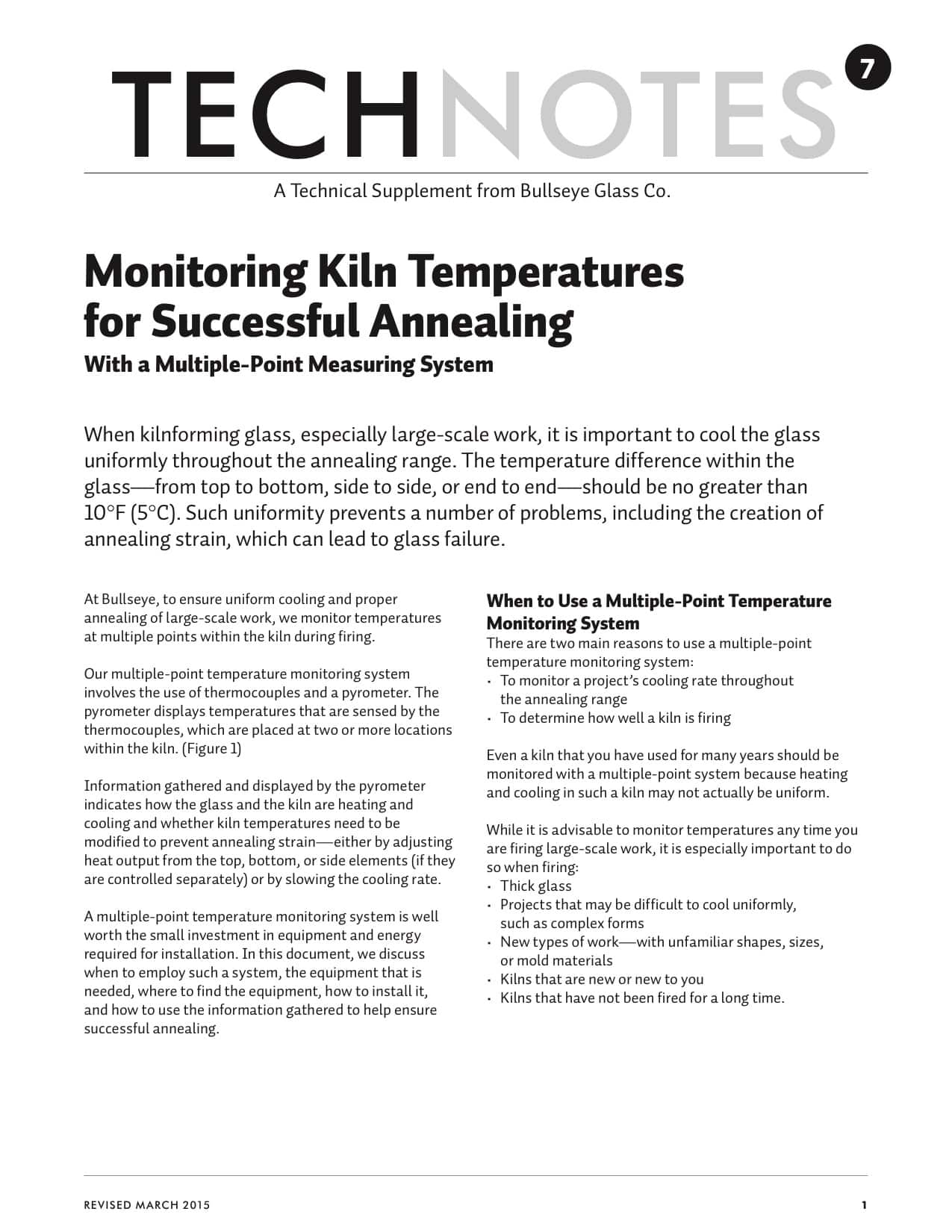